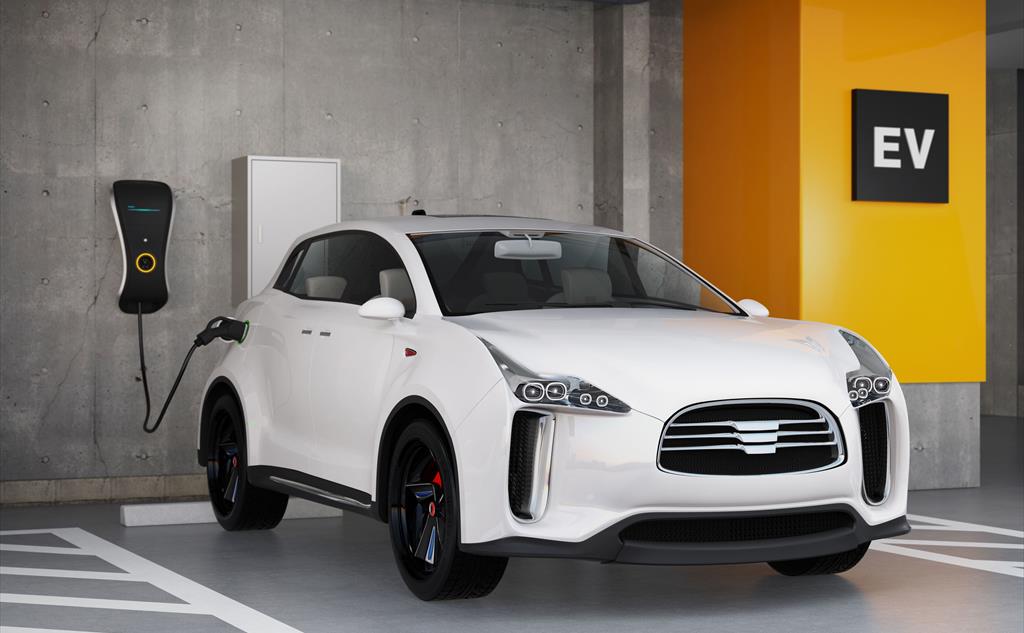
EV Batteries & EVSE
Although most major automotive OEMs are manufacturing electric vehicles (EVs) and consumer interest is growing – especially with all eyes on gas prices – several factors continue to inhibit widespread adoption. These include concerns about lithium-ion battery safety, vehicle range limits, and the availability and speed of charging infrastructure.
SABIC’s Specialties business offers a range of thermoplastic resins, compounds and copolymers that can help solve these challenges. Many of these materials have already been proven in the electrical/electronics industry. Further, SABIC has a long history of working collaboratively with the automotive industry on hybrids and battery electric vehicles. To assist customers, we offer resin customization capabilities, extensive application development and technical services, and a global production footprint.
To enhance EV safety, SABIC’s portfolio includes specialty materials that deliver halogen-free flame retardance, a balance of stiffness and ductility for energy absorption and crash protection, chemical resistance and thermal conductivity to enhance battery packs. Potential applications include module brackets and housings, electrical enclosures and frames, top and bottom enclosures, and corner support plates.
Weight reduction can help extend vehicle range. Our lightweight, high-performance thermoplastics can be considered to replace metal and other traditional materials. For example, NORYL GTX™ resins and LNP™ compounds and copolymers can be used in hybrid plastic/metal designs, such as lightweight honeycomb crash protection structures.
Low dielectric constant and dissipation factor (Dk/Df) are important properties for materials, such as LNP™ KONDUIT™ compounds and NORYL GTX™ resins, which are often used in battery thermal management and electrical insulation. Low dielectrics also come into play for sensors placed in the battery pack to monitor battery health and status. Still another potential application area is electrically insulative barriers and pads between battery components, such as cells and modules.
To help improve the speed and safety of EV charging, several of our specialty materials can be considered for both AC and fast DC charger components, such as panels, internal armature and charging connectors. These products feature weatherability, low water absorption, and resistance to high temperatures, impact and chemicals.
Featured Product Brands
LNP™ Compounds |
Specialty compounds based on 30 different resins and incorporating different fillers and additives to achieve various effects. |
NORYL™ Resins |
Modified PPE resins featuring high stiffness and strength, and good hydrolytic, chemical and creep resistance over a broad temperature range from - 40°C to +80°C and e-coat capable up to 220°C for up to 30 minutes. |
ULTEM™ Resins |
PEI resins known for an exceptionally low coefficient of thermal expansion (CTE), precise dimensions, plating capability, high heat resistance, broad chemical resistance, high strength and stiffness and metal replacement capabilities. |
LEXAN™ Copolymers |
PC-based copolymers featuring high impact, weatherability and chemical resistance. |
VALOX™ Resins |
PBT resins offering excellent chemical resistance and non-chlorinated/non-brominated flame retardance. |
EV Battery Components
SABIC’s specialty materials are well-suited for many different components in an EV battery pack. NORYL GTX™ resins can provide excellent energy absorption while minimizing weight compared to metal. NORYL™ resins deliver high stiffness and flame retardancy, helping to protect battery cells from impact and potential thermal runaway. Enclosures can benefit from the stiffness and light weight of NORYL™ resins and LNP™ compounds, while ULTEM™ resins can potentially replace metal in components that are exposed to extreme temperatures. All these materials also support design freedom for new battery configurations and the opportunity to incorporate thin walls that can help reduce weight and overcome space limitations.
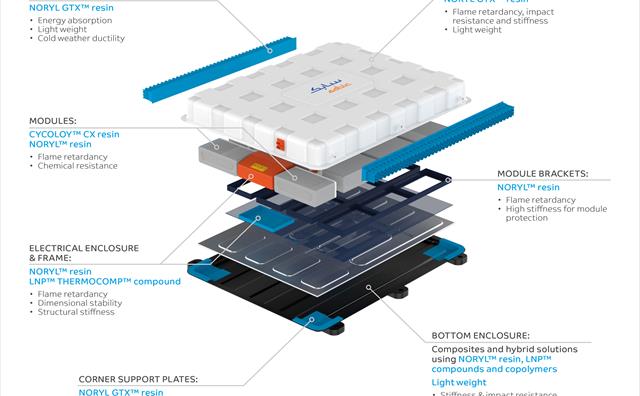
Featured Product Families
LNP™ THERMOCOMP™ Compounds |
provide heat resistance, dimensional stability and stiffness for potential applications such as electrical enclosures and frames in environments with high temperatures and chemical exposure. |
LNP KONDUIT™ Compounds |
are 10- to 50-times more thermally conductive than unfilled thermoplastics, making them well-suited for components like battery module housings that require heat dissipation/management. By conducting heat into a heat sink or the surrounding air, they help extend product life. |
NORYL GTX™ Resins |
are modified PPE resins with polyamide offering dimensional stability, low density, and good hydrolytic, chemical, temperature and creep resistance for potential components such as crash impact protection and battery top covers and corner support plates. They are also E-coat capable up to 220°C for up to 30 minutes. |
NORYL™ Resins |
are modified PPE materials that deliver low specific gravity, hydrolytic stability, good impact strength and good electrical properties and have the potential to be used for battery module housings and brackets, electrical enclosures and battery pack bottom enclosures. |
ULTEM™ Resins |
are amorphous PEI materials that deliver outstanding elevated thermal resistance, high strength and stiffness, and broad chemical resistance. They can potentially replace metal in busbars and castings. |
EVSE Components
In addition to federal and industry efforts to expand EVSE networks to accommodate more vehicles, there is strong demand from consumers, businesses and fleets for faster charging to save turnaround time. One approach is to replace alternating current (AC) chargers with direct current (DC) chargers, which provide power directly to the battery. Today’s DC chargers can give vehicles an 80% charge in approximately 1 hour. Some leading OEMs have deployed more than 30,000 DC Superchargers worldwide to serve customers.
To support fast/super-fast DC chargers, SABIC’s LNP™ THERMOCOMP™ compounds provide high temperature resistance and excellent insulative properties to withstand high voltages (440 – 800 V). Materials with low dielectric constant/dissipation factor (Dk/Df) properties, such as LNP™ KONDUIT™ compounds, can support faster transmission from charger to vehicle.
SABIC’s specialty materials can help address the need for additional charging stations by delivering key properties such as weatherability, low/high temperature resistance, and impact resistance to protect the charger from damage. For greater design flexibility, NORYL GTX™ resins are being considered as a potential replacement for polyamide in charger parts.
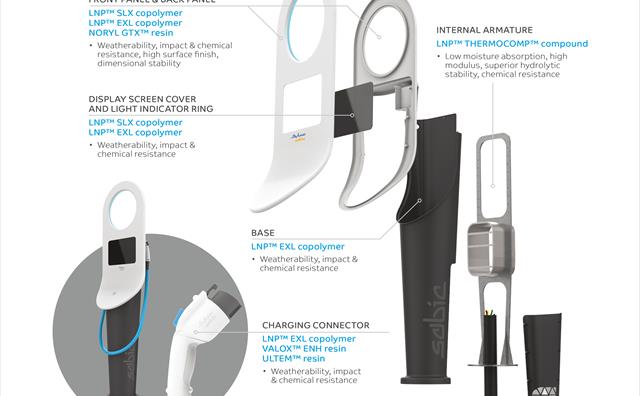
Featured Product Families
LNP™ THERMOCOMP™ Compounds |
provide heat resistance, dimensional stability and stiffness for internal armature exposed to environments with high temperatures and chemicals. |
NORYL GTX™ Resins |
are modified PPE resins with polyamide offering dimensional stability, low density, and good hydrolytic, chemical, temperature and creep resistance. They are well-suited for charger handles, bases and front/back panel housings, and are E-coat capable up to 220°C for up to 30 minutes. |
NORYL™ Resins |
are modified PPE materials that deliver low specific gravity, hydrolytic stability, good impact strength and good electrical properties over a broad temperature range from - 40°C to +80°C. They are well suited for internal electrical components. |
LNP™/LEXAN™ SLX Resins |
are weatherable, UV-resistant PC copolymer materials that provide excellent aesthetics, including super-high gloss and piano black colors, and are well-suited for front/back panel housings, display screen covers and light indicator rings. |
LNP™/LEXAN™ EXL Resins |
are high-impact PC-siloxane copolymer resins featuring excellent resistance to weather and chemicals. They are well-suited for wireless charging grounding assembly components due to their good impact resistance. Potential applications include charging connectors and unit bases. |
VALOX™ ENH Resins |
are injection moldable, 30% glass fiber-reinforced PBT resins with excellent chemical resistance and non-chlorinated/brominated flame retardance (meet UL94 V0 @ 0.80 mm and 5VA/5VB @ 1.5mm.). They are good candidates for applications like charging connectors that need a sustainable FR solution. |